In a photovoltaic power generation system, MC4 connectors are mainly used in components, combiner boxes, inverters, and the connections between them, most of which are installed in the factory, and the crimping quality is relatively reliable.
About 10% of the remaining connectors need to be manually installed at the project site, mainly referring to the need to install connectors at both ends of the photovoltaic cable connecting each device. According to the experience of many years of customer visits, due to the lack of training of on-site installation workers and the use of professional crimping tools, crimping irregularities are common, as shown below:
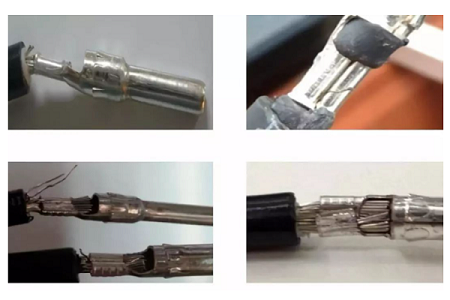
Types and characteristics of metal parts
The metal part is the main body of the connector and the most important flow path. At present, the vast majority of MC4 connectors on the market use a "U"-shaped metalcore, which is stamped and formed from a copper sheet, also known as a stamped metalcore. Thanks to the stamping process, the "U"-shaped metalcore not only has high production efficiency but also can be arranged in a chain, which is very suitable for automated wire harness production.
Some solar connectors use "O"-shaped metal cores, which are formed by drilling holes at both ends of thin copper rods, which are also called machined metal cores. The "O"-shaped metal core can only be crimped individually, which is not suitable for use in automated equipment.
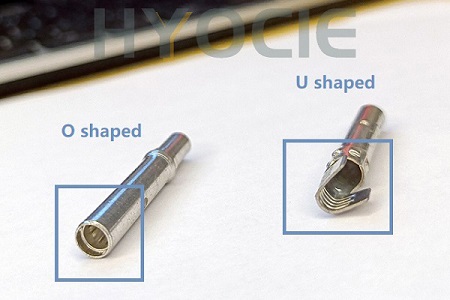
Our factory uses O shaped for 1500V, U shaped for 1000V.
The reliability of crimping largely depends on tools and operations, both of which determine whether the final crimping effect meets the requirements of the standard. Take the "U"-shaped metalcore as an example. It is basically a copper tin-plated material(Our 10mm2 MC4 metal parts are copper silver-plated) and needs to be connected to the photovoltaic cable by crimping. The crimping process is as follows:
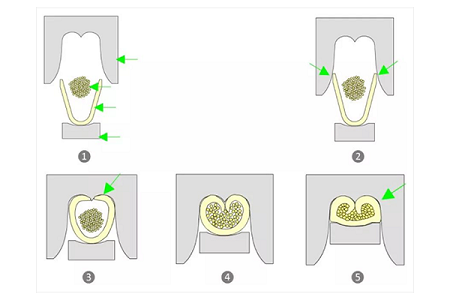
"U"-shaped metal core crimping is a process in which as the crimping height gradually decreases (while the crimping force gradually increases), the copper sheet wrapped with the copper wire of the cable is gradually compressed. In this process, the control of crimping height directly determines the quality of crimping. The control of the crimp width is not very important, because the crimp die determines the width value.
Crimping quality evaluation
1) The crimping height/width can be measured with a vernier caliper within the defined range
2)Pull-off force is the force required to pull or break the copper wire from the crimping place, such as a 4mm2 cable. IEC 60352-2 requires at least 310N
3) Resistance, taking 4mm2 cable as an example, IEC 60352-2 requires the resistance at the crimp to be less than 135 microohms
4) Cross-sectional analysis losslessly cut off the crimping zone, analyze width, height, compression rate, symmetry, cracks, burrs, etc.
If it is to release a new device or a new crimping die, in addition to the above points, it is also necessary to monitor the resistance stability under temperature cycling conditions, refer to the standard IEC 60352-2.
MC4 Connectors are small parts, but they will affect the operational efficiency of photovoltaic projects. Compromise with quality usually means high subsequent losses and risks, which could have been avoided.
Pls, choose us -HYOCIE, MC4 manufacturer in China.